The growing use of aluminum alloys in the aerospace and automotive industries has led to a search for ways to drill and mill this material quickly, efficiently and economically. In response to our many customers in these sectors, we have added drills, cutting inserts and endmills coated with DLC (Diamond-Like Carbon) to our product line. DLC is a unique thin coating composed mainly of carbon that features a high level of hardness, superior friction/wear properties and excellent adhesion resistance.
While working with aluminum creates some machining challenges, the positive properties of the material offset some of these difficulties.
Automotive: Weight Reduction
The use of aluminum alloys in the automotive industry is growing faster than any other use of the material. This boom is due to the increased demand for lightweight components and their implications in improving fuel economy, carbon neutrality and high performance. The mechanical properties of aluminum: high strength stiffness to weight ratio, good formability, excellent corrosion resistance and recycling potential make it the ideal candidate to replace heavier materials.
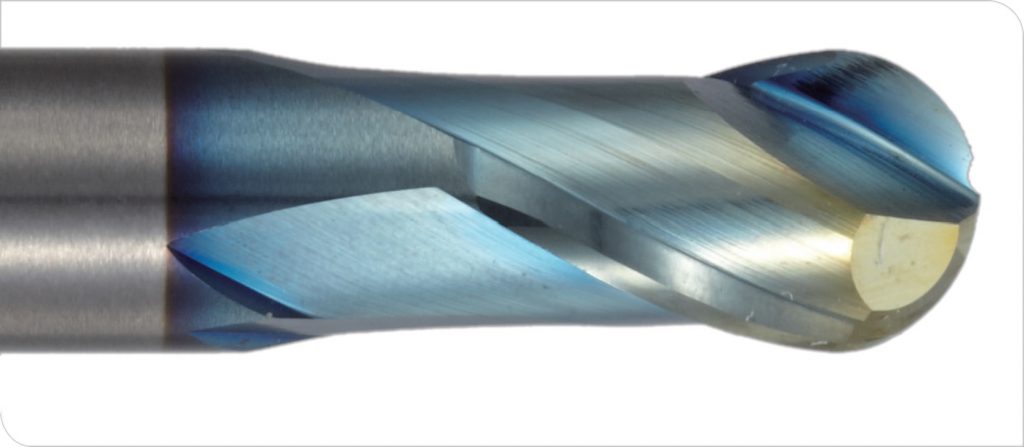
Aerospace: Low Density Strength
For aerospace applications, lightweight composites, alloys and carbon fibers have replaced aluminum for non-critical structural areas. However, aluminum is making a comeback with the help of titanium aluminide (TiAl) and aluminum lithium (Al-Li). This is due to their lower density and higher strength, as well as superior fatigue and corrosion resistance. Most commonly utilized in fuselage, wing and supporting-structure construction, these aluminum alloys offer a range of benefits for both aircraft and space flight engineering.
Customers Talk. We Listen.
The material shift in these two sectors is not only driving demand for aluminum, but pushing equipment and technology suppliers to step up and provide products that improve production and efficiency in manufacturing components made of the material. Listening to customer feedback is an integral part of our business model, and we saw the trend developing and responded quickly with our DLC offerings.
The DLC Difference
DLC coating has a low friction coefficient, which provides a definite advantage when machining non-ferrous materials. It has excellent adhesion resistance that results in superior chip evacuation with no curling on the body.
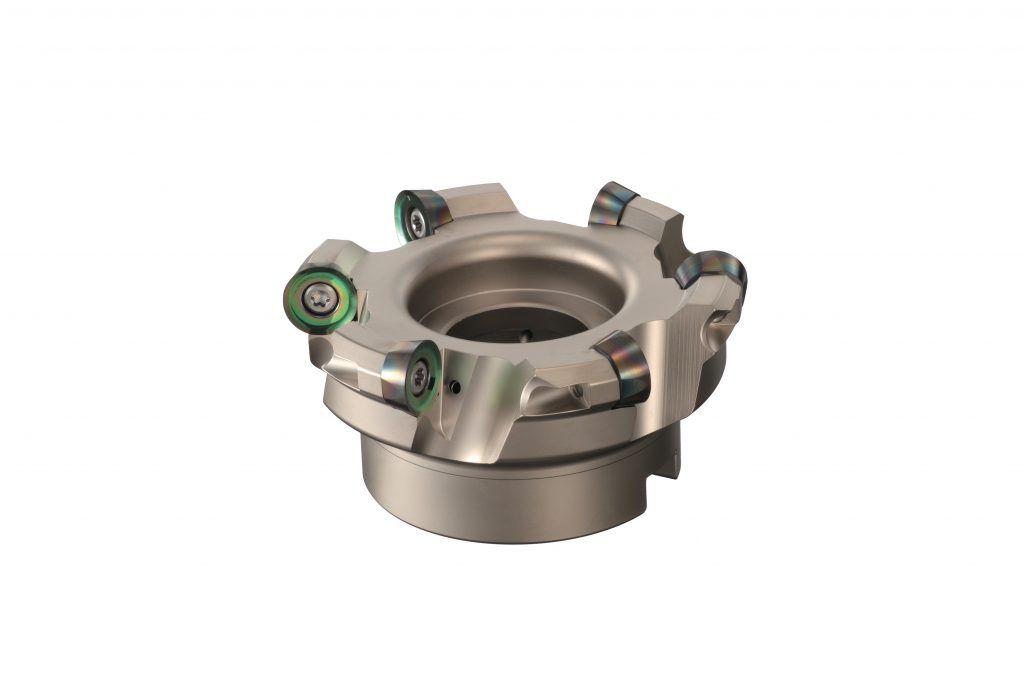
Tools coated with DLC have lower cutting forces compared to a normal cemented carbide tool in both wet and dry conditions. A 67% reduction in thrust provides higher efficiency drilling when compared to uncoated or diamond coated tools at 3-5 times the feed rate. The reduced cutting force also reduces surface roughness, eliminating the need for most additional deburring operations.
Extended tool life is another solid benefit of DLC Coating. In a test versus a competitor, tools coated with DLC increased tool life 119% and achieved 112.5% more parts per edge.
The Sumitomo DLC Line
We now offer a wide range of DLC products for most aluminum alloy machining applications.
Endmills:
- SBN Ball Nose Endmills
- ASM 2 Flute and 4 Flute Endmills
Milling Inserts:
- WAX Shoulder Milling Cutter
- WRCX Wave Radius Mill Series
- WEX Wave Mill Series
Drills:
- NHRF Type
- NHMF Type
- NHGS Type
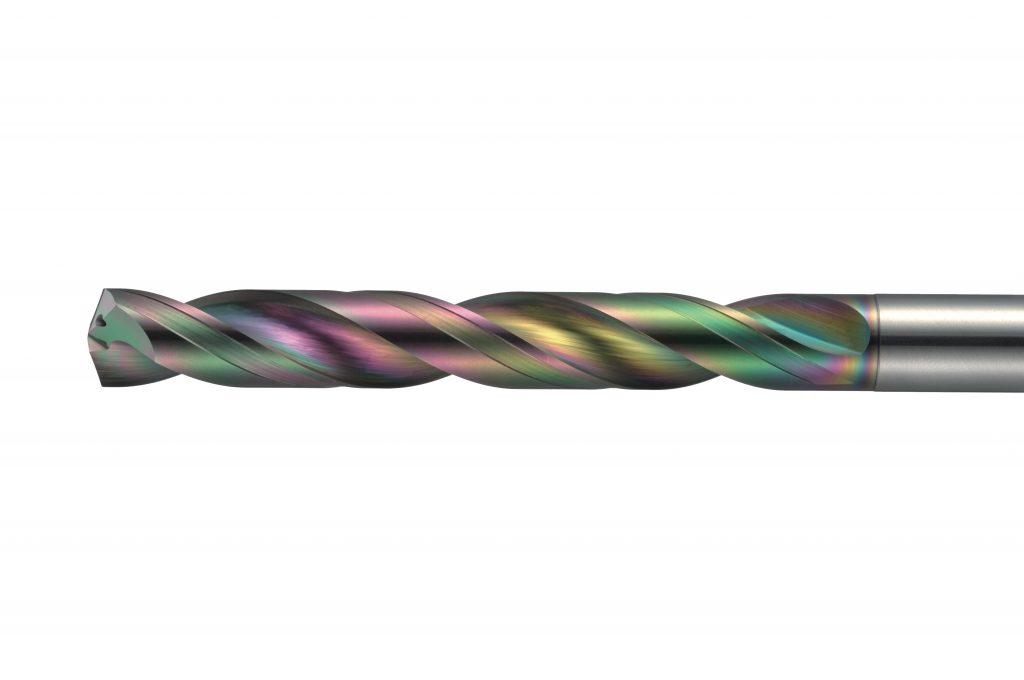
Some DLC Science
All the tools in our DLC line are coated in-house using the cathode arc PVD (Physical Vapor Deposition) method. This forms a DLC film on the surface of a substrate by generating a continuous vacuum charge on the surface of a solid graphite cathode to efficiently generate carbon ions. The process features easy formation of hard hydrogen-free DLC films that contain more diamond and less graphite because of the high vaporization and ionization rates of graphite. Suffice it to say that the result is a thin film with a hardness second only to diamond.
Reconditioning Used Tools
Bring new life into your used tools by sending them to us for a quality regrind and recoat in our brand new DLC coating chamber. It’s a great way to extend the productivity of your tools. Our certified regrind process will reduce your cost of production and waste, improving your profitability. Regrinding and recoating a tool provides almost the same thrust force as a new drill.
Aluminum alloys are indispensable to our automotive and aerospace customers. We will continue to partner with them to provide the best results when machining this challenging yet essential material. For more information about our complete line of DLC products or regrinds, please contact us for a consultation.